Key Points
- Coal is a combustible black or brownish-black sedimentary rock occurring in layers or veins called coal beds or coal seams. It is composed primarily of carbon, along with variable quantities of other elements, chiefly hydrogen, sulfur, oxygen, and nitrogen. A fossil fuel, coal forms from dead plant matter.
- Early coal extraction was small-scale, with coal lying either on the surface or very close to it. The early coal mining techniques left considerable amount of usable coal behind. Although some deep mining in Britain took place as early as the 1500s, deep shaft mining began to develop extensively in the late 18th century, with rapid expansion throughout the 19th century and early 20th century when the industry peaked. Coalfields helped to make the regions where they were located prosperous. Coal was so abundant in Britain that the supply could be stepped up to meet the rapidly rising demand.
- Coal was central to the development of the steam engine and, in turn, the steam engine dramatically increased the efficiency of coal mining. The introduction of the steam pump by Thomas Savery in 1698 and the Newcomen steam engine in 1712 greatly facilitated the removal of water from mines and enabled shafts to be made deeper, enabling more coal to be extracted. The next major step occurred when James Watt developed an improved version of Newcomen’s engine. Watt’s ten-horsepower engines enabled a wide range of manufacturing machinery to be powered.
- Coal mining remained very dangerous due to the presence of firedamp in many coal seams. Conditions of work were very poor, with a high casualty rate from rock falls. Coal mining has also been historically linked to bonded labor long after slavery was formally abolished in many parts of the world. Some of the worst abuses of child labor continued in coal mines. The miners, less affected by imported labor or machines than were the cotton mill workers, began to form trade unions and fight their grim battle for wages against the coal owners and royalty-lessees.
- The replacement of wood and other bio-fuels with coal was also a major change in the metal industries during the Industrial Revolution. For a given amount of heat, coal required much less labor than cutting wood and converting it to charcoal. Coal was also more abundant than wood. The reverberatory furnace technology, which keeps impurities in the coal from migrating into the metal, was highly advanced during the period. Coal was also central to the gas lighting industry.
- The origins of the environmental movement lay in the response to increasing levels of smoke pollution in the atmosphere during the Industrial Revolution. The emergence of large factories and corresponding immense growth in coal consumption gave rise to an unprecedented level of air pollution in industrial centers. The first non-governmental organizations and environment protection policies were a result of the development of coal-based industries during the Industrial Revolution.
Key Terms
- steam engine: A heat engine that performs mechanical work using steam.
- coke: A fuel with few impurities and a high carbon content, the solid carbonaceous material derived from destructive distillation of low-ash, low-sulfur bituminous coal. While it can form naturally, the common form is man-made.
- reverberatory furnace: A metallurgical or process furnace that isolates the material being processed from contact with the fuel, but not from contact with combustion gases. The term reverberation is used here in a generic sense of rebounding or reflecting, not in the acoustic sense of echoing.
Coal and Coal Mining in Britain
Coal is a combustible black or brownish-black sedimentary rock occurring in layers or veins called coal beds or coal seams. Coal is composed primarily of carbon, along with variable quantities of other elements, chiefly hydrogen, sulfur, oxygen, and nitrogen. A fossil fuel, coal forms when dead plant matter is converted into peat, which in turn is converted into lignite, then sub-bituminous coal, bituminous coal, and lastly anthracite. This involves biological and geological processes that take place over time.
The history of coal mining goes back thousands of years. Early coal extraction was small-scale, with coal lying either on the surface or very close to it. The early coal mining techniques left considerable amount of usable coal behind. Although some deep mining in Britain took place as early as the 1500s, deep shaft mining began to develop extensively in the late 18th century, with rapid expansion throughout the 19th century and early 20th century when the industry peaked. The location of the coalfields helped to make the prosperity of Lancashire, Yorkshire, and South Wales. Northumberland and Durham were the leading coal producers and the sites of the first deep pits. In much of Britain, coal was worked from drift mines or scraped off when it outcropped on the surface. Small groups of part-time miners used shovels and primitive equipment. As a result of these limited methods, in the deep Tyneside pits (300 to 1,000 ft deep) for example, only about 40 percent of the coal could be extracted.
Coal was so abundant in Britain that the supply could be increased to meet the rapidly rising demand. In 1700, the annual output of coal was just under 3 million tons. Between 1770 and 1780, the annual output of coal was some 6.25 million long tons (or about the output of a week and a half in the 20th century). After 1790 output soared, reaching 16 million long tons by 1815. By 1830 this rose to over 30 million tons.
Use of Coal During the Industrial Revolution
The development of the Industrial Revolution led to the large-scale use of coal as the steam engine took over from the water wheel. In 1700, five-sixths of the world’s coal was mined in Britain.
Steam Engine and Coal Mining
Coal was central to the development of the steam engine and in turn, the steam engine dramatically increased the efficiency of coal mining.
Before the steam engine, shallow bell pits followed a seam of coal along the surface, which were abandoned as the coal was extracted. In other cases, if the geology was favorable, the coal was mined by means of an adit or drift mine driven into the side of a hill. Shaft mining was done in some areas, but the limiting factor was the problem of removing water. It could be done by hauling buckets of water up the shaft or to a sough (a tunnel driven into a hill to drain a mine). In either case, the water had to be discharged into a stream or ditch at a level where it could flow away by gravity.
The introduction of the steam pump by Thomas Savery in 1698 and the Newcomen steam engine in 1712 facilitated the removal of water and enabled shafts to be made deeper so more coal could be extracted. A number of Newcomen engines were successfully put to use in Britain for draining hitherto unworkable deep mines, with the engine on the surface. These large machines, requiring a lot of capital to build, were extremely inefficient by modern standards, but greatly increased the scope of coal miningwhen located where coal was cheap at pit heads.
Despite their disadvantages, Newcomen engines were reliable and easy to maintain, and continued to be used in the coalfields until the early decades of the 19th century. The next major step occurred when James Watt developed (1763–1775) an improved version of Newcomen’s engine. Boulton and Watt ‘s early engines used half as much coal as John Smeaton’s improved version of Newcomen’s. Watt’s ten-horsepower engines could powera wide range of manufacturing machinery and be sited anywhere that water and coal or wood fuel could be obtained.
Coal mining remained very dangerous due to the presence of firedamp in many coal seams. Some degree of safety was provided by the safety lamp invented in 1816 by Sir Humphry Davy and independently by George Stephenson. However, the lamps proved a false dawn because they became unsafe very quickly and provided a weak light. Firedamp explosions continued, often setting off coal dust explosions, so casualties grew during the entire 19th century. Conditions of work were very poor, with a high casualty rate from rock falls.
Coal mining has also been historically linked to bonded labor long after slavery was formally abolished in many parts of the world. For example, Scottish miners had been bonded to their “masters” by a 1606 Act “Anent Coalyers and Salters.” A Colliers and Salters (Scotland) Act 1775, recognized this to be “a state of slavery and bondage” and formally abolished it. This decision was made effective by a further law in 1799. Some of the worst abuses of child labor continued in coal mines throughout the Industrial Revolution. The miners, less affected by imported labor or machines than were the cotton mill workers, began to form trade unions and fight their grim battle for wages against the coal owners and royalty-lessees. In South Wales, the miners showed a high degree of solidarity. They lived in isolated villages where they comprised the great majority of workers. There was a high degree of equality in lifestyle. Combined with an evangelical religious style based on Methodism, this led to forging a “community of solidarity” under the leadership of the Miners Federation.
Mining has always been dangerous because of methane gas explosions, roof cave-ins, and the difficulty of mine rescue. The worst single disaster in British coal mining history was at Senghenydd in the South Wales coalfield. In 1913 an explosion and subsequent fire killed 436 men and boys. The Courrières mine disaster, Europe’s worst mining accident, caused the death of 1,099 miners in Northern France in 1906.
Wagonways for moving coal in the mining areas started in the 17th century and were often associated with canal or river systems for the further movement of coal. These were all horse-drawn or relied on gravity, with a stationary steam engine to haul the wagons back to the top of the incline. The first applications of the steam locomotive were on wagon or plate ways (as they were then often called from the cast-iron plates used). Horse-drawn public railways did not begin until the early years of the 19th century when improvements to pig and wrought iron production lowered costs.
The development of the steam locomotive by Trevithick early in the 19th century gave added impetus and coal consumption grew rapidly as the railway network expanded through the Victorian period.
Metallurgy
The replacement of wood and other bio-fuels with coal was also a major change in the metal industries during the Industrial Revolution. For a given amount of heat, coal required much less labor to mine than cutting wood and converting it to charcoal, and coal was more abundant than wood.
Use of coal in smelting started somewhat before the Industrial Revolution, based on innovations by Sir Clement Clerke and others from 1678, using coal reverberatory furnaces known as cupolas. These were operated by the flames playing on the ore and charcoal or coke mixture, reducing the oxide to metal. This means that impurities (such as sulfur ash) in the coal do not migrate into the metal. This technology was applied to lead from 1678 and to copper from 1687. It was also applied to iron foundry work in the 1690s, but in this case the reverberatory furnace was known as an air furnace. This was followed by Abraham Darby, who made great strides using coke to fuel his blast furnaces at Coalbrookdale in 1709. Coke pig iron was hardly used to produce wrought iron in forges until the mid-1750s, when Abraham’s son, Abraham Darby II, built Horsehay and Ketley furnaces (not far from Coalbrookdale). By then, coke pig iron was cheaper than charcoal pig iron.
Gas Lighting
Another major industry of the later Industrial Revolution where coal was central was gas lighting. Although others made a similar innovation elsewhere, its large-scale introduction was the work of William Murdoch, an employee of Boulton & Watt, the steam engine pioneers. The process consisted of the large-scale gasification of coal in furnaces, the purification of the gas (removal of sulfur, ammonia, and heavy hydrocarbons), and its storage and distribution. The first gas lighting utilities were established in London between 1812 and 1820. They soon became one of the major consumers of coal in Britain. Gas lighting affected social and industrial organization because it allowed factories and stores to remain open longer than with tallow candles or oil. Its introduction allowed nightlife to flourish in cities and towns as interiors, and streets could be lighted on a larger scale than before.
Industrial Revolution, Coal, and Environmental Movement
The origins of the environmental movement lay in the response to increasing levels of smoke pollution in the atmosphere during the Industrial Revolution. The emergence of great factories and the concomitant immense growth in coal consumption gave rise to an unprecedented level of air pollution in industrial centers. After 1900 the large volume of industrial chemical discharges added to the growing load of untreated human waste. The first large-scale, modern environmental laws came in the form of Britain’s Alkali Acts, passed in 1863, to regulate the deleterious air pollution given off by the Leblanc process used to produce soda ash.
Levels of air pollution rose during the Industrial Revolution, sparking the first modern environmental laws to be passed in the mid-19th century.
In industrial cities, local experts and reformers, especially after 1890, took the lead in identifying environmental degradation and pollution and initiating grass-roots movements to demand and achieve reforms. Typically the highest priority was water and air pollution. The Coal Smoke Abatement Society was formed in Britain in 1898 making it one of the oldest environmental non-governmental organizations (NGOs). It was founded by artist Sir William Blake Richmond, who was frustrated with the pall cast by coal smoke. Although there were earlier pieces of legislation, the Public Health Act of 1875 required all furnaces and fireplaces to consume their own smoke. It also provided for sanctions against factories that emitted large amounts of black smoke.
Key Points
- Early iron smelting used charcoal as both the heat source and the reducing agent. By the 18th century, the availability of wood for making charcoal limited the expansion of iron production, so England became increasingly dependent on imports from Sweden and Russia. Smelting with coal (or its derivative coke ) was a long-sought objective, with some early advancements ٞachieved throughout the 17th century. Britain’s demand for iron and steel, combined with ample capital and energetic entrepreneurs, rapidly made it the world leader of metallurgy.
- A major change in the metal industries during the era of the Industrial Revolution was the replacement of wood and other bio-fuels with coal. Use of coal in smelting started somewhat before the Industrial Revolution, based on innovations by Sir Clement Clerke and others from 1678, using coal reverberatory furnaces known as cupolas. With cupolas, impurities in the coal did not migrate into the metal.
- Abraham Darby made great strides using coke to fuel his blast furnaces at Coalbrookdale in 1709. However, coke pig iron was hardly used to produce wrought iron in forges until the mid-1750s, when his son Abraham Darby II built Horsehay and Ketley furnaces. Since cast iron was becoming cheaper and more plentiful, it became a structural material following the building of the innovative Iron Bridge in 1778 by Abraham Darby III.
- Wrought iron for smiths to forge into consumer goods was still made in finery forges, as it long had been. However, new processes were adopted in the ensuing years. The first is referred to today as potting and stamping, but this was superseded by Henry Cort’s puddling process. Cort developed two significant iron manufacturing processes: rolling in 1783 and puddling in 1784. Rolling replaced hammering for consolidating wrought iron and expelling some of the dross. Rolling was 15 times faster than hammering with a trip hammer.
- Hot blast, patented by James Beaumont Neilson in 1828, was the most important development of the 19th century for saving energy in making pig iron. By using waste exhaust heat to preheat combustion air, the amount of fuel to make a unit of pig iron was reduced.
- The supply of cheaper iron aided a number of industries. The development of machine tools allowed better working of iron, increasing its use in the rapidly growing machinery and engine industries. Prices of many goods decreased, making them more available and common.
Key Terms
- coke: A fuel with few impurities and a high carbon content, usually made from coal. It is the solid carbonaceous material derived from destructive distillation of low-ash, low-sulfur bituminous coal. While it can be formed naturally, the commonly used form is man-made.
- pig iron: An intermediate product of the iron industry. It has a very high carbon content, typically 3.5–4.5%, along with silica and other constituents of dross, which makes it very brittle and not useful as a material except in limited applications. It is made by smelting iron ore into a transportable ingot of impure high carbon-content iron as an ingredient for further processing steps. It is the molten iron from the blast furnace, a large cylinder-shaped furnace charged with iron ore, coke, and limestone.
- Iron Bridge: A bridge that crosses the River Severn in Shropshire, England. Opened in 1781, it was the first arch bridge in the world to be made of cast iron and was greatly celebrated after construction.
- reverberatory furnaces: A metallurgical or process furnace that isolates the material being processed from contact with the fuel, but not from contact with combustion gases. The term reverberation is used here in a generic sense of rebounding or reflecting, not in the acoustic sense of echoing.
Iron and Industrial Revolution in Britain
Early iron smelting used charcoal as both the heat source and the reducing agent. By the 18th century, the availability of wood for making charcoal had limited the expansion of iron production, so England became increasingly dependent on Sweden (from the mid-17th century) and then from about 1725 on Russia for the iron required for industry. Smelting with coal (or its derivative coke) was a long-sought objective. The production of pig iron with coke was probably achieved by Dud Dudley in the 1620s, and with a mixed fuel made from coal and wood again in the 1670s. However this was only a technological rather than a commercial success. Shadrach Fox may have smelted iron with coke at Coalbrookdale in Shropshire in the 1690s, but only to make cannonballs and other cast iron products such as shells. In the time of peace, they did not enjoy much demand.
Britain’s demand for iron and steel, combined with ample capital and energetic entrepreneurs, rapidly made it the world leader of the metallurgy. In 1875, Britain accounted for 47% of world production of pig iron and almost 40% of steel. Forty percent of British output was exported to the U.S., which was rapidly building its rail and industrial infrastructure. The growth of pig iron output was dramatic. Britain went from 1.3 million tons in 1840 to 6.7 million in 1870 and 10.4 in 1913.
Technological Advancements
A major change in the metal industries during the era of the Industrial Revolution was the replacement of wood and other bio-fuels with coal. For a given amount of heat, coal required much less labor to mine than cutting wood and converting it to charcoal, and coal was more abundant than wood. Use of coal in smelting started before the Industrial Revolution based on innovations by Sir Clement Clerke and others from 1678, using coal reverberatory furnaces known as cupolas. These were operated by the flames playing on the ore and charcoal or coke mixture, reducing the oxide to metal. This has the advantage that impurities such as sulfur ash in the coal do not migrate into the metal. This technology was applied to lead from 1678 and to copper from 1687. It was also applied to iron foundry work in the 1690s, but in this case the reverberatory furnace was known as an air furnace. The foundry cupola is a different (and later) innovation.
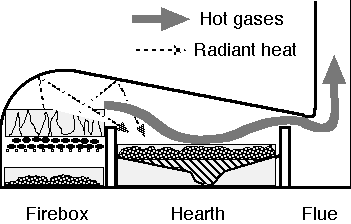
Abraham Darby made great strides using coke to fuel his blast furnaces at Coalbrookdale in 1709. However, the coke pig iron he made was used mostly for the production of cast iron goods, such as pots and kettles. He had the advantage over his rivals in that his pots, cast by his patented process, were thinner and cheaper than theirs. Coke pig iron was hardly used to produce wrought iron in forges until the mid-1750s, when his son Abraham Darby II built Horsehay and Ketley furnaces. By then, coke pig iron was cheaper than charcoal pig iron. Since cast iron was becoming cheaper and more plentiful, it became a structural material following the building of the innovative Iron Bridge in 1778 by Abraham Darby III.
The Iron Bridge crosses the River Severn in Shropshire, England, and is the first bridge in the world to be made of cast iron. During the winter of 1773–74, local newspapers advertised a proposal to petition Parliament for leave to construct an iron bridge with a single 120 feet (37 m) span. In 1775, Abraham Darby III, the grandson of Abraham Darby I and an ironmaster working at Coalbrookdale, was appointed treasurer to the project.
Wrought iron for smiths to forge into consumer goods was still made in finery forges, as it long had been. However, new processes were adopted in the ensuing years. The first is referred to today as potting and stamping, but this was superseded by Henry Cort’s puddling process. Cort developed two significant iron manufacturing processes: rolling in 1783 and puddling in 1784. Rolling replaced hammering for consolidating wrought iron and expelling some of the dross. Rolling was 15 times faster than hammering with a trip hammer. Roller mills were first used for making sheets, but also rolled structural shapes such as angles and rails.
Puddling produced structural-grade iron at a relatively low cost. It was a means of decarburizing pig iron by slow oxidation, with iron ore as the oxygen source, as the iron was manually stirred using a long rod. Puddling was done in a reverberatory furnace, allowing coal or coke to be used as fuel.
The decarburized iron, having a higher melting point than cast iron, was raked into globs by the puddler. When the glob was large enough, the puddler would remove it. Puddling was backbreaking and extremely hot work. Few puddlers lived to age 40. The process continued ntil the late 19th century when iron was displaced by steel. Because puddling required human skill in sensing the iron globs, it was never successfully mechanized.
Hot blast, patented by James Beaumont Neilson in 1828, was the most important development of the 19th century for saving energy in making pig iron. By using waste exhaust heat to preheat combustion air, the amount of fuel to make a unit of pig iron was reduced at first by between one-third using coal or two-thirds using coke. However, the efficiency gains continued as the technology improved. Hot blast also raised the operating temperature of furnaces, increasing their capacity. Using less coal or coke meant introducing fewer impurities into the pig iron. This meant that lower quality coal or anthracite could be used in areas where coking coal was unavailable or too expensive.
The supply of cheaper iron aided a number of industries, such as those making nails, hinges, wire, and other hardware items. The development of machine tools allowed better working of iron, leading to increased use in the rapidly growing machinery and engine industries. Iron was used in agricultural machines, making farm labor more effective. The new technological advancements were also critical to the development of the rail. Prices of many goods, such as iron cooking utensils, decreased, making them more available and commonly used.
Key Points
- Steel is an alloy of iron and other elements, primarily carbon, that is widely used in construction and other applications because of its high tensile strength and low cost. Steel’s base metal is iron. It was first produced in antiquity, but two decades before the Industrial Revolution an improvement was made in the production of steel, which at the time was an expensive commodity used only where iron would not do.
- Benjamin Huntsman developed his crucible steel technique in the 1740s. He was able to make satisfactory cast steel in clay pot crucibles, each holding about 34 pounds of blister steel. A flux was added, and they were covered and heated by coke for about three hours. The molten steel was then poured into molds and the crucibles reused. For a long time Huntsman exported his whole output to France as local producers refused to work with steel harder than they were already using.
- Steel is often cited as the first of several new areas for industrial mass-production that characterize the Second Industrial Revolution. Before about 1860, steel was still an expensive product. The problem of mass-producing cheap steel was solved in 1855 by Henry Bessemer with the introduction of the Bessemer converter at his steelworks in Sheffield, England. Further experiments by Göran Fredrik Göransson and Robert Forester Mushet allowed Bessemer to perfect what would be known as the Bessemer process.
- Although initially Bessemer met with rebuffs and was forced to undertake the exploitation of his process himself, eventually licences were applied for in such numbers that Bessemer received royalties exceeding a million pounds sterling. By 1870, Bessemer steel was widely used for ship plate. The Bessemer process also made steel railways competitive in price. Experience quickly proved steel had much greater strength and durability and could handle the heavier and faster engines and cars.
- After 1890, the Bessemer process was gradually supplanted by open-hearth steel making. Carl Wilhelm Siemens developed the Siemens regenerative furnace in the 1850s. This furnace operated at a high temperature by using regenerative preheating of fuel and air for combustion. In 1865, Pierre-Émile Martin took out a license from Siemens and applied his regenerative furnace for making steel. The Siemens-Martin process was slower and thus easier to control. It also permitted the melting and refining of large amounts of scrap steel, further lowering steel production costs and recycling an otherwise troublesome waste material.
- The Siemens-Martin process became the leading steel-making process by the early 20th century. The availability of cheap steel allowed larger bridges, railroads, skyscrapers, and ships. Other important steel products were steel cable, steel rod, and sheet steel, which enabled large, high-pressure boilers and high-tensile strength steel for machinery. Military equipment also improved significantly.
Key Terms
- cementation: An obsolete technology for making steel by carburization of iron. Unlike modern steel making, it increased the amount of carbon in the iron. It was apparently developed before the 17th century. Derwentcote Steel Furnace, built in 1720, is the earliest surviving example of a furnace using this technology.
- carburization: A heat treatment process in which iron or steel absorbs carbon while the metal is heated in the presence of a carbon-bearing material, such as charcoal or carbon monoxide. The intent is to make the metal harder. Unlike modern steel making, the process increased the amount of carbon in the iron.
- crucible steel: A term that applies to steel made by two different methods in the modern era and produced in varying locales throughout history. It is made by melting iron and other materials. It was produced in South and Central Asia during the medieval era but techniques for production of high-quality steel were developed by Benjamin Huntsman in England in the 18th century. However, Huntsman’s process used iron and steel as raw materials rather than direct conversion from cast iron as in the later Bessemer process. The homogeneous crystal structure of this cast steel improved its strength and hardness compared to preceding forms of steel.
- Bessemer process: The first inexpensive industrial process for the mass production of steel from molten pig iron before the development of the open hearth furnace. The key principle is removal of impurities from the iron by oxidation with air blown through the molten iron. The oxidation also raises the temperature of the iron mass and keeps it molten.
- Second Industrial Revolution: A phase of rapid industrialization in the final third of the 19th century and the beginning of the 20th, also known as the Technological Revolution. Although a number of its characteristic events can be traced to earlier innovations in manufacturing, such as the establishment of a machine tool industry, the development of methods for manufacturing interchangeable parts, and the invention of the Bessemer Process, it is generally dated between 1870 and 1914 up to the start of World War I.
Steel and the Industrial Revolution
Steel is an alloy of iron and other elements, primarily carbon, that is widely used in construction and other applications because of its high tensile strength and low cost. Steel’s base metal is iron, which is able to take on two crystalline forms, body-centered cubic (BCC) and face-centered cubic (FCC), depending on its temperature. It is the interaction of those allotropes with the alloying elements, primarily carbon, that gives steel and cast iron their range of unique properties. In the BCC arrangement, there is an iron atom in the center of each cube, and in the FCC, there is one at the center of each of the six faces of the cube. Carbon, other elements, and inclusions within iron act as hardening agents that prevent the movement of dislocations that otherwise occur in the crystal lattices of iron atoms.
Steel (with lower carbon content than pig iron but higher than wrought iron) was first produced in antiquity, but two decades before the Industrial Revolution an improvement was made in the production of steel, which at the time was an expensive commodity used only where iron would not do, such as for cutting-edge tools and for springs. Benjamin Huntsman developed his crucible steel technique in the 1740s. After many experiments, Huntsman was able to make satisfactory cast steel in clay pot crucibles, each holding about 34 pounds of blister steel. A flux was added, and they were covered and heated by coke for about three hours. The molten steel was then poured into molds and the crucibles reused. The local cutlery manufacturers refused to buy Huntsman’s cast steel, as it was harder than the German steel they were accustomed to using. For a long time Huntsman exported his whole output to France. Blister steel used by Huntsman as raw material was made by the cementation process or by carburization of iron. Carburization is a heat treatment process, in which iron or steel absorbs carbon while the metal is heated in the presence of a carbon-bearing material, such as charcoal or carbon monoxide. The intent is to make the metal harder. Unlike modern steel making, the process increased the amount of carbon in the iron.
Second Industrial Revolution
Steel is often cited as the first of several new areas for industrial mass-production that characterize the Second Industrial Revolution beginning around 1850, although a method for mass manufacture of steel was not invented until the 1860s and became widely available in the 1870s after the process was modified to produce more uniform quality.
Before about 1860, steel was an expensive product, made in small quantities and used mostly for swords, tools, and cutlery. All large metal structures were made of wrought or cast iron. The problem of mass-producing cheap steel was solved in 1855 by Henry Bessemer with the introduction of the Bessemer converter at his steelworks in Sheffield, England. In the Bessemer process, molten pig iron from the blast furnace was charged into a large crucible, and air was blown through the molten iron from below, igniting the dissolved carbon from the coke. As the carbon burned off, the melting point of the mixture increased, but the heat from the burning carbon provided the extra energy needed to keep the mixture molten. After the carbon content in the melt dropped to the desired level, the air draft was cut off. A typical Bessemer converter could convert a 25-ton batch of pig iron to steel in half an hour. Bessemer demonstrated the process in 1856 and had a successful operation going by 1864.
Although the Bessemer process is no longer commercially used, at the time of its invention it was of enormous industrial importance because it lowered the cost of production steel, leading to steel being widely substituted for cast iron.Bessemer’s attention was drawn to the problem of steel manufacture in an attempt to improve the construction of guns.
Bessemer licensed the patent for his process to five ironmasters, but from the outset, the companies had great difficulty producing good quality steel. Göran Fredrik Göransson, a Swedish ironmaster, using the purer charcoal pig iron of that country, was the first to make good steel by the process, but only after many attempts. His results prompted Bessemer to try a purer iron obtained from Cumberland hematite, but had only limited success because the quantity of carbon was difficult to control. Robert Forester Mushet, after thousands of experiments at Darkhill Ironworks, had shown that the quantity of carbon could be controlled by removing almost all of it from the iron and then adding an exact amount of carbon and manganese in the form of spiegeleisen (a ferromanganese alloy). This improved the quality of the finished product and increased its malleability.
When Bessemer tried to induce makers to take up his improved system, he met with general rebuffs and was eventually driven to undertake the exploitation of the process himself. He erected steelworks in Sheffield in a business partnership with others, such as W & J Galloway & Sons, and began to manufacture steel. At first the output was insignificant, but gradually the magnitude of the operation was enlarged until the competition became effective and steel traders became aware that the firm of Henry Bessemer & Co. was underselling them to the extent of UK£10-£15 a ton. This argument to the pocket quickly had its effect, and licenses were applied for in such numbers that, in royalties for the use of his process, Bessemer received a sum considerably exceeding a million pounds sterling. By 1870, Bessemer steel was widely used for ship plate. By the 1850s, the speed, weight, and quantity of railway traffic was limited by the strength of the wrought-iron rails in use. The solution was to turn to steel rails, which the Bessemer process made competitive in price. Experience quickly proved steel had much greater strength and durability and could handle the heavier and faster engines and cars.
However, Mushet received nothing and by 1866 was destitute and in ill health. In that year his 16-year-old daughter, Mary, traveled to London alone to confront Bessemer at his offices, arguing that his success was based on the results of her father’s work. Bessemer decided to pay Mushet an annual pension of £300, a very considerable sum, which he did for over 20 years, possibly to keep the Mushets from legal action.
After 1890, the Bessemer process was gradually supplanted by open-hearth steel making. Sir Carl Wilhelm Siemens developed the Siemens regenerative furnace in the 1850s and claimed in 1857 to be recovering enough heat to save 70–80% of the fuel. This furnace operated at a high temperature by using regenerative preheating of fuel and air for combustion. In regenerative preheating, the exhaust gases from the furnace are pumped into a chamber containing bricks, where heat is transferred from the gases to the bricks. The flow of the furnace is then reversed so that fuel and air pass through the chamber and are heated by the bricks. Through this method, an open-hearth furnace can reach temperatures high enough to melt steel, but Siemens did not initially use it for that. In 1865, the French engineer Pierre-Émile Martin took out a license from Siemens and first applied his regenerative furnace for making steel. The most appealing characteristic of the Siemens regenerative furnace is the rapid production of large quantities of basic steel, used for example to construct high-rise buildings.
The most appealing characteristic of the Siemens regenerative furnace was the rapid production of large quantities of basic steel, used for example to construct high-rise buildings. Through Siemens’ method, an open-hearth furnace could reach temperatures high enough to melt steel, but Siemens did not initially use it for that. It was Martin who first applied the regenerative furnace for making steel.
The Siemens-Martin process complemented rather than replaced the Bessemer process. It was slower and thus easier to control. It also permitted the melting and refining of large amounts of scrap steel, further lowering steel production costs and recycling an otherwise troublesome waste material. Its worst drawback was and remains the fact that melting and refining a charge takes several hours. Furthermore, the work environment around an open hearth furnace was and remains extremely dangerous.
The Siemens-Martin process became the leading steel making process by the early 20th century. The availability of cheap steel allowed larger bridges, railroads, skyscrapers, and ships. Other important steel products—also made using the open hearth process—were steel cable, steel rod, and sheet steel which enabled large, high-pressure boilers and high-tensile strength steel for machinery, creating much more powerful engines, gears, and axles than were previously possible. With large amounts of steel, it also became possible to build much more powerful guns and carriages, tanks, armored fighting vehicles, and naval ships.
Text adapted from Boundless World History. Revisions and additions by History Guild.
Provided by: Boundless.com. License: CC BY-SA: Attribution-ShareAlike
CC LICENSED CONTENT, SPECIFIC ATTRIBUTION
Coal. Provided by: Wikipedia. Located at: https://en.wikipedia.org/wiki/Coal. License: CC BY-SA: Attribution-ShareAlike
Reverberatory furnace. Provided by: Wikipedia. Located at: https://en.wikipedia.org/wiki/Reverberatory_furnace. License: CC BY-SA: Attribution-ShareAlike
History of coal miners. Provided by: Wikipedia. Located at: https://en.wikipedia.org/wiki/History_of_coal_miners. License: CC BY-SA: Attribution-ShareAlike
History of coal mining. Provided by: Wikipedia. Located at: https://en.wikipedia.org/wiki/History_of_coal_mining. License: CC BY-SA: Attribution-ShareAlike
Steam engine. Provided by: Wikipedia. Located at: https://en.wikipedia.org/wiki/Steam_engine. License: CC BY-SA: Attribution-ShareAlike
Industrial Revolution. Provided by: Wikipedia. Located at: https://en.wikipedia.org/wiki/Industrial_Revolution. License: CC BY-SA: Attribution-ShareAlike
Coal mining in the United Kingdom. Provided by: Wikipedia. Located at: https://en.wikipedia.org/wiki/Coal_mining_in_the_United_Kingdom. License: CC BY-SA: Attribution-ShareAlike
Coke (fuel). Provided by: Wikipedia. Located at: https://en.wikipedia.org/wiki/Coke_(fuel). License: CC BY-SA: Attribution-ShareAlike
StRolloxChemical_1831.jpg. Provided by: Wikipedia. Located at: https://en.wikipedia.org/wiki/File:StRolloxChemical_1831.jpg. License: Public Domain: No Known Copyright
Courriu00e8res_1906_LeJ.jpg. Provided by: Wikimedia Commons. Located at: https://commons.wikimedia.org/wiki/File:Courri%C3%A8res_1906_LeJ.jpg. License: Public Domain: No Known Copyright
Ferrous metallurgy. Provided by: Wikipedia. Located at: https://en.wikipedia.org/wiki/Ferrous_metallurgy. License: CC BY-SA: Attribution-ShareAlike
Industrial Revolution. Provided by: Wikipedia. Located at: https://en.wikipedia.org/wiki/Industrial_Revolution. License: CC BY-SA: Attribution-ShareAlike
History of the steel industry (1850u20131970). Provided by: Wikipedia. Located at: https://en.wikipedia.org/wiki/History_of_the_steel_industry_(1850%E2%80%931970). License: CC BY-SA: Attribution-ShareAlike
Pig iron. Provided by: Wikipedia. Located at: https://en.wikipedia.org/wiki/Pig_iron. License: CC BY-SA: Attribution-ShareAlike
The Iron Bridge. Provided by: Wikipedia. Located at: https://en.wikipedia.org/wiki/The_Iron_Bridge. License: CC BY-SA: Attribution-ShareAlike
Reverberatory furnace. Provided by: Wikipedis. Located at: https://en.wikipedia.org/wiki/Reverberatory_furnace. License: CC BY-SA: Attribution-ShareAlike
Coke (fuel). Provided by: Wikipedia. Located at: https://en.wikipedia.org/wiki/Coke_(fuel). License: CC BY-SA: Attribution-ShareAlike
Iron. Provided by: Wikipedia. Located at: https://en.wikipedia.org/wiki/Iron. License: CC BY-SA: Attribution-ShareAlike
StRolloxChemical_1831.jpg. Provided by: Wikipedia. Located at: https://en.wikipedia.org/wiki/File:StRolloxChemical_1831.jpg. License: Public Domain: No Known Copyright
Courriu00e8res_1906_LeJ.jpg. Provided by: Wikimedia Commons. Located at: https://commons.wikimedia.org/wiki/File:Courri%C3%A8res_1906_LeJ.jpg. License: Public Domain: No Known Copyright
The_Iron_Bridge_8542.jpg. Provided by: Wikimedia Commons. Located at: https://commons.wikimedia.org/wiki/File:The_Iron_Bridge_(8542).jpg. License: CC BY-SA: Attribution-ShareAlike
Reverberatory_furnace_diagram.png. Provided by: Wikimedia Commons. Located at: https://commons.wikimedia.org/wiki/File:Reverberatory_furnace_diagram.png. License: CC BY-SA: Attribution-ShareAlike
Open hearth furnace. Provided by: Wikipedia. Located at: https://en.wikipedia.org/wiki/Open_hearth_furnace. License: CC BY-SA: Attribution-ShareAlike
Reverberatory furnace. Provided by: Wikipedia. Located at: https://en.wikipedia.org/wiki/Reverberatory_furnace. License: CC BY-SA: Attribution-ShareAlike
Benjamin Huntsman. Provided by: Wikipedia. Located at: https://en.wikipedia.org/wiki/Benjamin_Huntsman. License: CC BY-SA: Attribution-ShareAlike
Industrial Revolution. Provided by: Wikipedia. Located at: https://en.wikipedia.org/wiki/Industrial_Revolution. License: CC BY-SA: Attribution-ShareAlike
Second Industrial Revolution. Provided by: Wikipedia. Located at: https://en.wikipedia.org/wiki/Second_Industrial_Revolution. License: CC BY-SA: Attribution-ShareAlike
Cementation process. Provided by: Wikipedia. Located at: https://en.wikipedia.org/wiki/Cementation_process. License: CC BY-SA: Attribution-ShareAlike
Steel. Provided by: Wikipedia. Located at: https://en.wikipedia.org/wiki/Steel. License: CC BY-SA: Attribution-ShareAlike
History of the steel industry (1850u20131970). Provided by: Wikipedia. Located at: https://en.wikipedia.org/wiki/History_of_the_steel_industry_(1850%E2%80%931970). License: CC BY-SA: Attribution-ShareAlike
Ferrous metallurgy. Provided by: Wikipedia. Located at: https://en.wikipedia.org/wiki/Ferrous_metallurgy. License: CC BY-SA: Attribution-ShareAlike
Spiegeleisen. Provided by: Wikipedia. Located at: https://en.wikipedia.org/wiki/Spiegeleisen. License: CC BY-SA: Attribution-ShareAlike
Bessemer process. Provided by: Wikipedia. Located at: https://en.wikipedia.org/wiki/Bessemer_process. License: CC BY-SA: Attribution-ShareAlike
Carburizing. Provided by: Wikipedia. Located at: https://en.wikipedia.org/wiki/Carburizing. License: CC BY-SA: Attribution-ShareAlike
Crucible steel. Provided by: Wikipedia. Located at: https://en.wikipedia.org/wiki/Crucible_steel. License: CC BY-SA: Attribution-ShareAlike
Henry Bessemer. Provided by: Wikipedia. Located at: https://en.wikipedia.org/wiki/Henry_Bessemer. License: CC BY-SA: Attribution-ShareAlike
StRolloxChemical_1831.jpg. Provided by: Wikipedia. Located at: https://en.wikipedia.org/wiki/File:StRolloxChemical_1831.jpg. License: Public Domain: No Known Copyright
Courriu00e8res_1906_LeJ.jpg. Provided by: Wikimedia Commons. Located at: https://commons.wikimedia.org/wiki/File:Courri%C3%A8res_1906_LeJ.jpg. License: Public Domain: No Known Copyright
The_Iron_Bridge_8542.jpg. Provided by: Wikimedia Commons. Located at: https://commons.wikimedia.org/wiki/File:The_Iron_Bridge_(8542).jpg. License: CC BY-SA: Attribution-ShareAlike
Reverberatory_furnace_diagram.png. Provided by: Wikimedia Commons. Located at: https://commons.wikimedia.org/wiki/File:Reverberatory_furnace_diagram.png. License: CC BY-SA: Attribution-ShareAlike
Siemensmartin12nb.jpg. Provided by: Wikimedia Commons. Located at: https://commons.wikimedia.org/wiki/File:Siemensmartin12nb.jpg. License: Public Domain: No Known Copyright
ConverterB.jpg. Provided by: Wikimedia Commons. Located at: https://commons.wikimedia.org/wiki/File:ConverterB.jpg. License: Public Domain: No Known Copyright